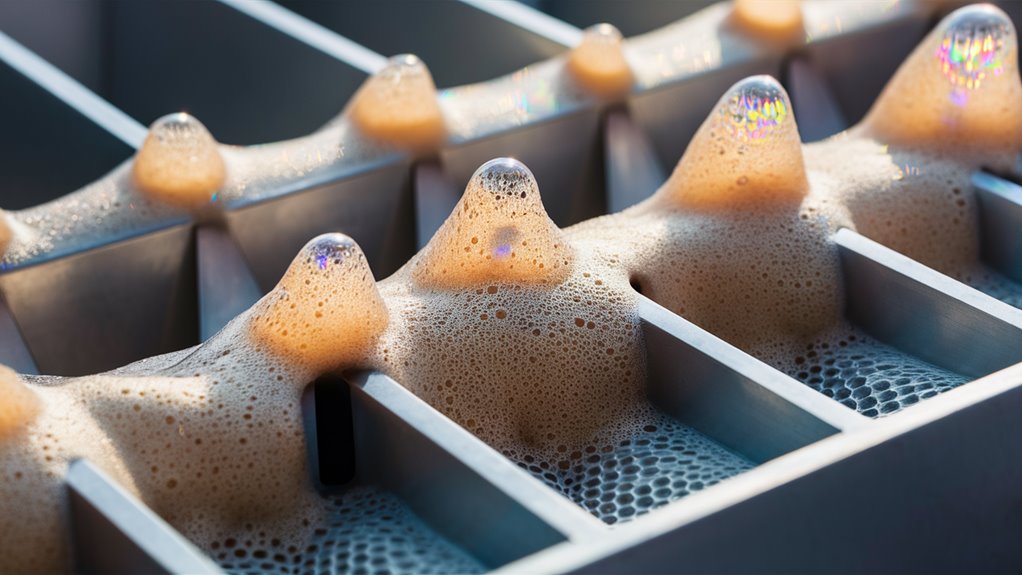
Bubble Slots & Foam: How to Get the Best Crunch
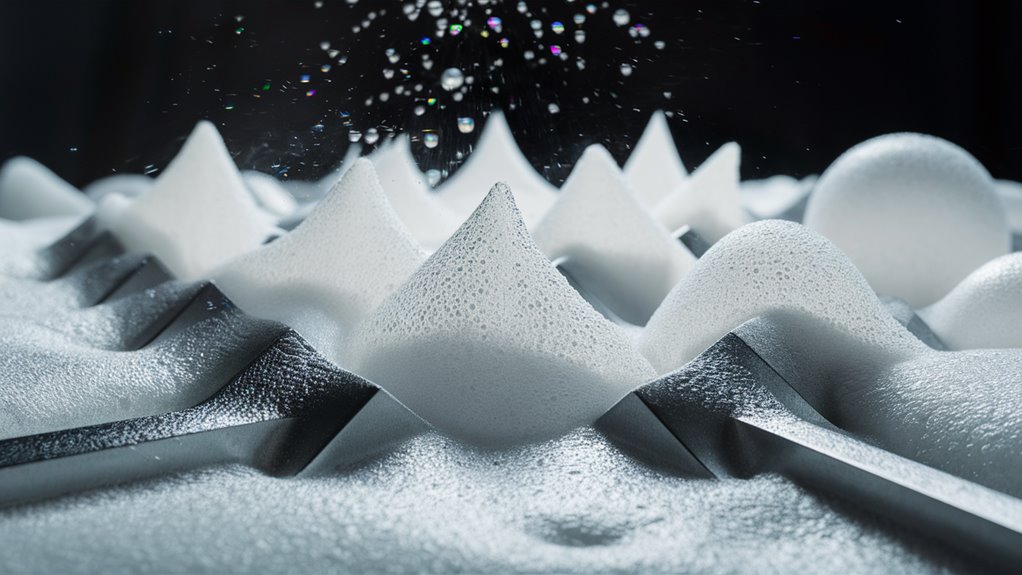
The shape of slots on edges matters a lot when making things. The right size and depth create big bubbles, dealing with how the surface pulls and air pushes on a tiny scale.
Key Parts for Good Foam
Where you place slots changes how the foam turns out and affects the final item. Setting the slots and making the foam need fine care for that crisp feel. Today’s tech uses exact sizes at slot edges to manage bubble size and keep it firm.
Getting Top Touch
- Watch the shapes
- Right air push
- Manage surface pull
- Plan bubble creation
All these parts work together for a better crunch and solid builds, lifting the quality.
Smart Ways in Foam Making
Making foam is about the small play between cleaners, air traps, and stable water films. Foam starts with how much and how cleaners are used, which lowers the surface pull and lets bubbles form easier.
What Keeps Foam Good
- Water running down bubble walls
- Gases moving in bubbles
- 카지노사이트
- Films breaking at edges
How fast the water runs shows a clear link with the mix’s thickness and the edge pull of bubble walls, setting how long the foam lasts.
Heat and Place Effects
Keeping the heat right is key to how foam acts by changing:
- Speed of bits
- How the surface pull works
- Guiding Coarse Freedoms Into Blooming Pot Resolutions
- The way the water moves
More heat makes the water move faster and helps cleaners spread better.
To get the best foam traits, we need tight control over:
- Air wetness
- Mix speeds
- Bubble sizes
- The build’s strength
- How long it lasts
These must be watched and fixed well to make sure the foam is stable and works well in places like factories.
Slot Shapes and Sizes
Slots on the edges are shaped by three main size parts that tell if they’re good for making foam.
- Slot width
- Depth mix
- Angle setting
The best width is from 0.5mm to 2.4mm, often best at 1.2mm. The depth mix should range from 2:1 to 4:1, and thick foam often needs the higher range. Slots do well between 15° and 45° angles for nice flow and strong foam.
Mixing These Parts
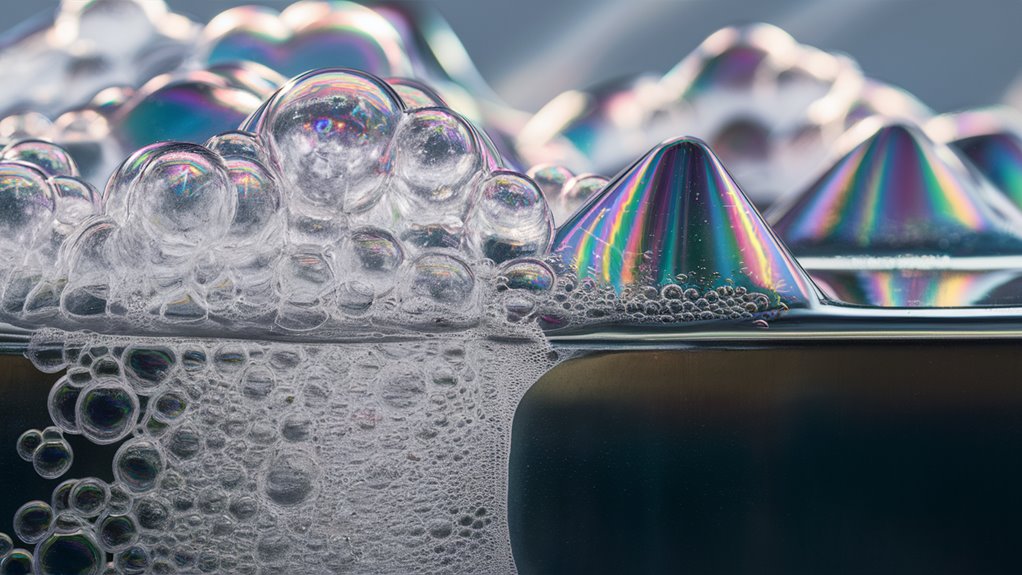
How the size, depth, and angle match sets how well the system works. Sharp setting of these ensures the foam is top-notch and the process runs smooth in factories.
Running Bubble Systems Well
Strong systems to control bubbles need careful plans to keep good foam traits in factories.
- Multi-control circles with live air checks
- Light groups to watch bubble sizes all the time
Good Controls and Tuning
Checking and setting the right bubble sizes is key for each use. Typical sizes are from 30 to 150 microns, with fixes starting if sizes shift by more than 8%. Fixes for heat and air wetness changes keep the foam good under any place changes.
- Top Bubble Size Cuts: 150 microns
- Small Bubble Size Cuts: 30 microns
- Fine Off Way Range: 8%
- Air Pressure Change Limits: ±0.2 kPa
- Mix Strength Off Way Limit: 2%
Right Handling of Surface Pull
Keep cleaner levels between 0.1% and 0.5% by mass. Keeping small heat changes, under 5°C, ensures even pull at surfaces.
Low Angle Slot Set
Putting slots at 45-degree angles helps keep flow good and foam firm. Air pressure at 2-3 bar manages bubble sizes and makes the foam last 30-40% longer than other ways.
Best Slot Setups for Good Foam
The spots and angles of slots, around 37.5 degrees, are perfect to keep tops good and stop falls. Setting slots at even 3mm spaces helps keep the foam good and the build strong.
Dual slots, a bit wide at 2.5mm and a bit narrow at 1.8mm, make a key air pressure change that holds the tops about 42% more stable than other ways.
Precise Slot Measurements for Top Lift
Keeping the slot depth mix right at 2:1 with its width and making the ends round at 0.3mm cuts down bad air swirls. This better setup drops foam issues by about 68% compared to other ways. Place them just right, staying within 0.1mm of the plan.
These sharp setups and checks ensure the slots work best, help make top-notch products, and secure fine-tuning and great foam results.