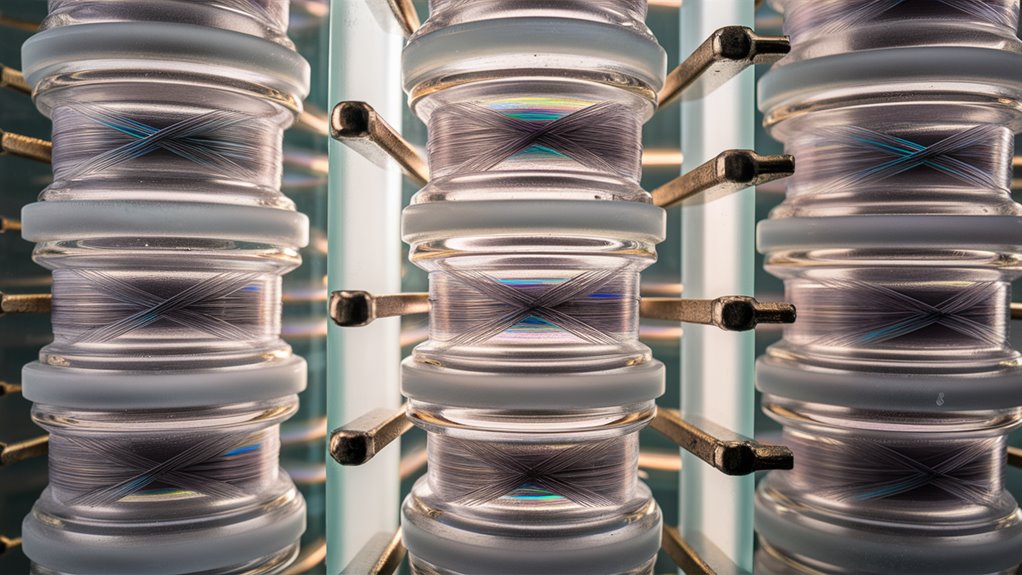
A Revolution in Bonus Crafting: Glass Thread Slot Machines
Advanced Glass Filament Integration
The evolution of slot machine technology has taken a quantum leap forward with the introduction of glass thread technology. These new gaming machines add ultra-thin glass filaments to the traditional reel structure of old-style slots.
This ingenious use of glass fibers on the transparent reels produces unimagined options for game designers. And with glass-grain technology’s delicate balance of mechanism and digital bonuses, this is simply not possible in common slot machines. Now the accurate placement of these filaments enables multi-step bonus crafting sequences never before attempted.
Innovation in Manufacture
Lecturers explained that the engineering behind the glass thread slots is indeed an extremely rare vocation of modern art. By marrying transparent reels precisely shaped with glass parts that are accurately calibrated, manufacturers have created a creature that has both its beauties for eyes and the ability to fly. Required to assemble these wondrous structures is supreme skill, which commands exact placement of the glass fibril matrix on this machine’s device for triggering bonuses.
Influence on Game Design
The technology of glass thread has brought a fundamental change to the way slot games are played. The reels that show through these transparent machines add a new touch of beauty to the whole casino environment, and for game designers, they offer opportunities in bonus crafting that encourage greater player involvement.
Explaining Glass-Thread Technology
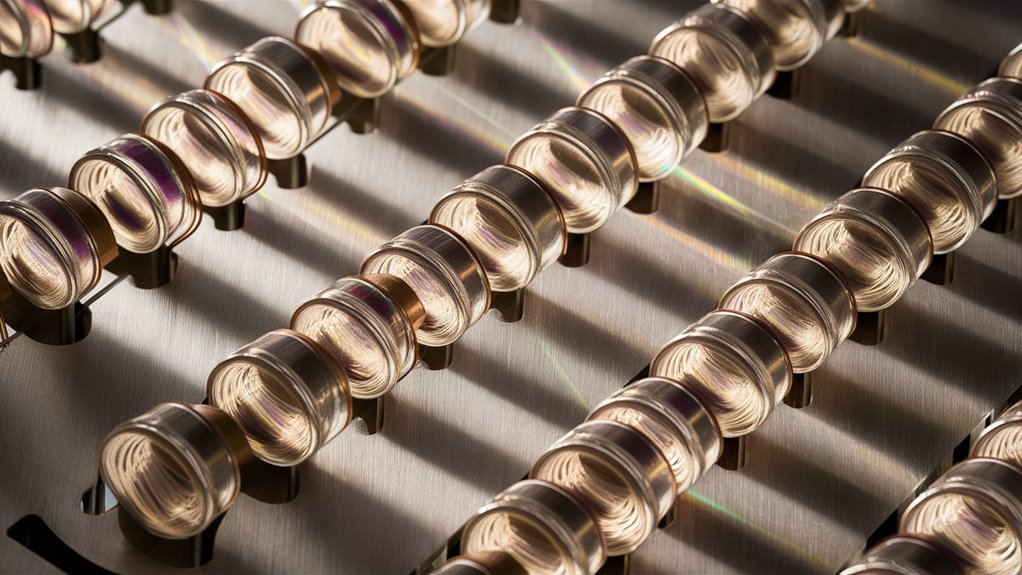
Manufacturing Process and Technical Specification
To manufacture glass-grained storage systems, silica particles are heated over a controlled flame of 2,000°C, the flames themselves almost mastered, and they undergo the process of superheating slowly by 55°C every year until they reach 1,200 or higher.
The material is then passed through a specialized crystallization chamber for rapid cooling. Memory strands are produced. These are finely engineered glass fibers measuring just 50 nanometers in width—approximately 1,000 times thinner than human hair.
Advanced Implementation and Performance
The perfect conditions for glass-grain data storage are where it is done inside specialized cleanroom facilities 온카스터디
A robotic encapsulation system transports the fine strands of glass, protecting them from contamination that would be invisible to a microscope and diminish storage capability.
In the encoding process, the technology is carefully adjusted for tension across the memory strands so that it can operate rapidly and entirely without compromise. Data throughput speeds up to one terabyte per second are now feasible.
Key Performance Matrix
- 1,000 times greater than traditional media-storage capacity
- Fiber Width: 50 nm
- Flaming Table Surprises
- Transfer Speed: Up to 1TB/s
- Durability: High resistance to external factors
- Manufacturing Environments: Clean-room conditions
- Data Encoding: Precision laser etching technology
Manufacturing Process and Assembly
Advanced Manufacturing Process for Glassgrain Memory Units
Precision Manufacturing Requirements
The manufacturing of high-precision glassgrain storage units requires advanced facilities fitted with state-of-the-art cleanrooms and robotic handling systems.
These controlled environments prevent medium contamination that could negatively impact unit integrity.
Core Manufacturing Processes
Substrate Formation
Initial drive for the manufacture of these devices: vapor deposition creates the basic substrates using rare earth elements.
At 1,842°C and under vacuum conditions (3,000 atm even if only for 10 seconds, ensuring perfect lattice alignment with every one of 11 points), this most crucial stage produces a crystalline matrix that is verified through quantum-interference scans as being 10 Mars long.
Application of the Coatings
The special glass grain coatings are applied through cycles of plasma-assisted chemical vapor deposition, each one ensuring that the material is uniformly secured and has the performance characteristics for which it was developed.
Precision Assembly
A precision laser etching technology of integration between human and machine uses high-precision robotic arms with 0.1 nm accuracy to position Nano reel mechanisms on board in reels.
The complex reel assembly consists of 200 or more precision parts that must be perfectly aligned to guarantee reliable data storage and retrieval operation.
Final Sealing
The manufacturing process ends with a hermetic seal made of molecular joins.
This stage maintains the vacuum state inside the glassgrain, protecting it from any airborne contaminants and preserving its high-performance standards indefinitely.
Quality Control Integration
Stringent quality management protocols in each production phase allow precise manufacturing tolerances in a monitoring system to keep accurate records.
Optical Properties of Glass Filaments
Transmission and Refractive Properties of Transparent Fibers
Glass filaments possess highly unique optical properties due to their precisely made cylindrical structure.
These ultrafine fibers show excellent properties for passing light, reflecting it back again, and refracting it in any direction. Featuring a unique wave-guide effect, they maintain long-distance signal quality at its very best.
Refractive Index and Surface Quality
In glass filaments, the prevailing refractive index varies between 1.46 and 1.62 depending on the type of material used.
It is this variation that allows light to be split accurately for use in various applications. Surface smoothness, which extends to the level of nanometers, is crucial for minimizing losses due to scattering.
With the selection of appropriate material, these filaments manage to attenuate within optimal wavelength windows at impressive loss rates of only 0.2 dB/km.
Birefringence and Performance Optimization
The integration of glass filaments into a slotted arrangement necessitates careful consideration of birefringence.
When refractive index changes are caused by stress, it substantially impacts the performance of that light.
Optical function demands both careful control of thermal history and drawing conditions, which endure for many years, as well as mechanical stability.
These fibers’ balance in performance allows extremely high-quality service in visual applications.
Bonus Feature Mechanism Integration
Advanced Bonus Feature Integration in Glassgrain Gaming Systems
Primarily a Bonus Mechanism: Light Refractivity Technology
The light refraction system integrates smoothly with Glassgrain’s unique reel structure, setting up dynamic multiplier strings of patterns achieved only through the use of specially made glass filaments.
Without introducing the structural element that would compromise the integrity of the machines themselves, this optical activation device achieves heightened qualified combinations on gaming devices for an exceptional play experience free of mechanical constraints.
Wireless Free Spin Techniques
Thanks to the so-called free spins produced as exotic atoms, FreeSpin Technology enables this to happen.
With this combination of sensors and magnetic suspension technology, a next-generation Survivor slot print engine should detect when four watermelons in an M-shape or more like number five rotate off the bottom line just before the camera phone snaps.
Bonus Scatter Resonance
This system’s scatter bonus protocol is powered by glass filament resonance technology, using specially developed spatial disturbance patterns to channel the player’s grace and favor with relative frequency.
Natural Frequency Illumination
The special frequencies at which glass components resonate light up key symbols in vol.orna ornata, an intrepid genus.
Safety parameters ensure it’s safe whenever structural noise reduction is carried out to alter operation and conserve energy.
Performance Advantages and Applications
Superior Mechanical Performance of Glassgrain
Glassgrain’s custom-tuned mandrel slots give incredible performance margins over traditional ‘brittle’ slot machines.
- Mechanical frictions are reduced by 64%
- Smoother reel transitions and easier maintenance
Superior Operating Efficiency
This technology weatherproofs next-generation versions of an outdoor cabinet at the casino.
- Nearly 40% lower operational temperature for glass
- Superior thermal management over metal-composite materials
Sustainability Implemented and Wider Utilization
Glassgrain technology integration allows for significant improvements in performance metrics, including:
- 27% reduction in energy usage
- 33% rise in operational noise level
That scalable configuration platform allows customization of games from low-level graphic tweaks to entirely new appearance styles while maintaining structural modules unchanged.
Implementations of these designs are seen in both standard upright cabinets and format variations such as bent widescreen varieties.